Getting Produce Safely from A to B — From an FCL Expert
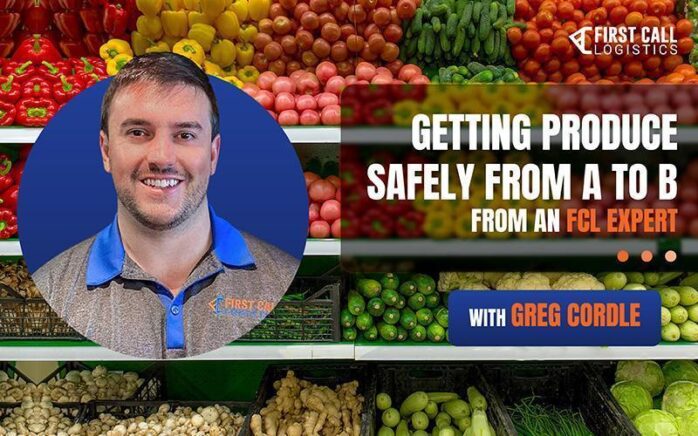
There’s a certain measure of expertise required to ensure fresh produce arrives on time and is properly preserved for grocery store shelves and restaurant kitchens throughout the year. In the field of logistics, it pays to work with experts well-versed in the intricacies of temperature-controlled freight who can identify efficient delivery methods, keep drivers and customers satisfied, and consistently avoid letting products spoil in transit.
We sat down with our own produce account management specialist, Greg Cordle, to ask a few questions about the cold chain, the logistics behind fresh produce, and what it’s like to race against the clock each day in his specialized role.
Getting to Know Our Expert in Produce Account Management Greg Cordle
A career in logistics likely wasn’t on Greg’s radar. However, after earning his degree in economics, Greg dove headfirst into an opportunity to work with some of the nation’s largest produce and agriculture vendors. Never one to ignore a challenge, Greg has thrived in the field of logistics and the high-pressure business of dealing exclusively with temperature-controlled vendors since 2014. Greg is now one of First Call’s go-to resources for produce account management.
Why Shipping Produce Is Its Own Special Challenge
Putting together moving pieces in efficient and timely ways is the hallmark of the entire logistics industry — only in cases of produce, the stakes can mean entirely ruined shipments if not handled with the proper care. The ins and outs of successful produce shipping include all the requisite communication and time management skills of a traditional logistics role, with the added challenge of temperature-controlled environments from the moment produce is harvested to the time it hits the shelves.
“First understand that produce starts going bad as soon as it leaves the ground,” Greg says. “The big-picture goal of the produce industry is to have the freshest and best-looking produce on the shelves at grocery stores (or in the kitchens at restaurants). Some commodities are more time-sensitive than others, but everything will start showing signs of decay eventually. So, the faster you can get it from field to table, the better.”
While time is the enemy of all logistical operations, there are additional considerations at work when shipping produce across the country. This includes the seasonality and shifting geography of many commodities’ origins, hazardous weather patterns, and several points along the cold chain where entire shipments can spoil.
“Time is the first big thing that contributes to the decay of produce, but the other big thing is temperature,” Greg says. “Different commodities have different ranges of acceptable temperatures — anything running too cold will begin to show signs of freeze damage or (if run too cold) can completely freeze. If a commodity is run too warm, the effects may not be seen as quickly, but most receivers will easily spot scarring, bruising, and sunken spots and reject the shipment.”
This is why keeping the cold chain intact is so important — regardless of how many trucks, cold storages, or sets of hands a product experiences, maintaining optimal temperature ranges is just as critical as delivery to the correct destination.
Attention to Detail Is Crucial in the World of Produce
The need to ensure produce remains safely within its required temperature ranges adds a major twist to an already fast-paced and challenging role. Greg’s responsibilities include not only finding the fastest and most cost-effective shipping lanes for large shipments of produce but pairing commodities with other compatible shipments based on their respective temperature requirements.
For an added challenge, products with precise requirements are frequently subject to approximate shipping and loading times, which can disrupt the produce’s necessary temperature ranges significantly.
“Just because a shipper might load trucks on a first come first serve basis, doesn’t mean that’s entirely true. Estimated ready times are just that — estimated. In situations with a tight timeline, a shipper may try to shorten the cooling process (or in some cases skip the cooling process altogether). The reefer units on the trucks we hire are built to be able to hold product at a specific temperature, but they cannot actually cool the product if it’s not loaded at proper temps. It’s important for our carriers to check this at the time of loading so we don’t run into issues at delivery.”
Keeping Produce Fresh in Transit
There are a few important requirements somewhat unique to the produce trucking industry as compared to other refrigerated commodities. First, all reefers must have air chutes that are fully intact and functioning. An air chute is essentially a plastic lining running along the inner top of the trailer distributing cold air throughout the trailer and maintaining the same amount of cool air along with the nose, middle, and tail of the trailer. Persistent checking and re-checking properly functioning air chutes eliminates one potential headache for produce in transit — but of course, there are several others that can creep in if shippers aren’t careful. Second, “We always run the reefer on the continuous temperature setting as opposed to the stop/start setting — sure that will save fuel, but it can be damaging to the produce since it allows the temperature in the trailer to fluctuate.
Even the best-laid plans are subject to accidents and disasters. In Greg’s case, a full-on truck breakdown is close to a nightmare scenario.
“In the unfortunate event of breakdown where a truck or trailer may be out of service for an extended period of time, it’s important to find a cross-docking facility that can unload and reload a new truck in an environment suitable to that particular commodity’s acceptable temperature range.”
Identifying Skills Needed to Succeed in Produce Account Management
The logistics of produce management calls on a variety of important skills, but like other experts we’ve interviewed for insights into what makes a good logistics professional tick, Greg confirms the most important attribute of all:
“The ability to communicate effectively and problem-solve. You might have to re-route at the last minute. You might have a truck break down on you. Being able to communicate exactly what’s going on throughout that process to all parties involved is critical.”
Additionally, the produce industry requires a thorough understanding of specific requirements for dozens of common commodities — requirements Greg says good account managers need to soak up and make second nature to their everyday dealings to keep up with the time-sensitivity of the job.
Why Greg Loves the High-Stakes Shipping Role
The advantages of Greg’s role might best be summarized as high-risk, high reward. In addition to higher commissions for dealing with temperature-sensitive freight, the thrill factor of delivering products to local groceries — and knowing he helped get them there — is difficult to match.
“Being the person a customer calls in a crunch, at the last minute, and knowing they might have brokers and carriers who may even be able to do it cheaper than I can, but that I can be trusted to make it happen — that’s what I like most,” Greg says. “I love earning that reputation for being there to save somebody in a crunch. That, and walking through a Kroger and seeing my customers’ product on the shelf and then taking it home and cooking it — I bought one of my customers’ asparagus last night.”
Make Your Career GO! at First Call Logistics
Want to build a career somewhere you can make a real impact? Consider joining the team at First Call Logistics. As a fast-growing 3PL, we’re expanding our footprint and hiring for multiple roles. To learn more about our open opportunities, visit our careers page and apply today!
Join The First Call Crew
Want to build a career somewhere you can make a real impact? Consider joining the team at First Call Logistics. As a fast-growing 3PL, we’re expanding our footprint and hiring for multiple roles.
To learn more about our open opportunities, visit our careers page and apply today!
Insights from FCL Experts
As a customer-focused company, we strive to provide detailed supply chain insights for all potential partners. Take an inside look at how our team solves real-world logistical challenges here:
- Article: How Produce Transport Works (and Why You’ll Want an Expert)
- Article: An Introduction to Temperature-Controlled Shipping
- Article: Refrigerated LTL Shipments: What You Need to Know
- Article: What It’s Like to Work with Temperature-Controlled Freight
- Article: Effective LTL Freight Strategies with Brock Hubble
- Article: Careers In Logistics: Q&A with First Call’s Tarek Kabbani
Get the latest supply chain news and updates directly to your inbox.